Process of anodized aluminum plate typically includes the following steps:
- Preparation of substrate: Firstly, it is necessary to select a suitable aluminum alloy plate as the substrate, and then carry out surface treatment, such as degreasing, decontamination, acid washing, etc.
- Pre-treatment before anodizing: The surface-treated aluminum plate is processed by etching, deburring, cleaning, etc., to ensure that the oxide film formed after anodizing is uniform and dense.
- Anodizing: The pre-treated aluminum plate is placed in an electrolyte containing sulfuric acid, oxalic acid, etc., and a layer of oxide film is formed on the surface of the aluminum plate through electrolysis. The thickness of the oxide film can be controlled by adjusting the temperature, concentration, current density, time and other parameters of the electrolyte.
- Sealing treatment: After anodizing, many small oxide holes will be formed on the surface of the oxide film. These holes can be filled to improve the sealing and corrosion resistance of the oxide film. A commonly used method is to put the oxide film in hot water or steam for sealing treatment.
- Dyeing treatment: The color of the anodized aluminum plate can be changed by dyeing the oxide film. Organic dyes are generally used, and the aluminum plate is immersed in the dye to penetrate into the oxide film and form the desired color.
- Final treatment: Finally, the dyed aluminum plate is cleaned, dried, etc. to ensure surface quality and performance.
The above is the general production process of anodized aluminum plate, and different manufacturers or products may have some differences.
Here are some common processing and treatment methods for anodized aluminum:
Cutting: Anodized aluminum can be cut using various methods, such as sawing, shearing, or laser cutting, depending on the thickness and shape of the material.
Bending: Anodized aluminum can be bent into different shapes using press brakes, rollers, or other tools. However, the bending process may cause cracks or damage to the anodized surface, which may need to be re-anodized after bending.
Welding: Anodized aluminum can be welded using various methods, including TIG welding, MIG welding, or resistance welding, but the anodized layer in the heat-affected zone may be damaged and require re-anodizing.
Machining: Anodized aluminum can be machined to create complex shapes and precision parts using techniques such as CNC milling, turning, or drilling. However, the machining process may remove the anodized layer, which may need to be reapplied after machining.
Surface treatment: Anodized aluminum can be further treated to improve its surface properties, such as coloring, polishing, or printing.
Forming: Anodized aluminum can be formed into different shapes using processes such as extrusion or casting. However, the anodized layer may be damaged during the forming process and require re-anodizing.
Heat treatment: Anodized aluminum can be heat-treated to improve its strength, hardness, or other properties, such as annealing, quenching, or tempering. However, the anodized layer may be damaged during the heat treatment process and require re-anodizing.
Joining: Anodized aluminum parts can be joined together using various methods, including mechanical fastening, adhesives, or riveting.
Here are some common application areas of anodized aluminum:
Architecture: Anodized aluminum is commonly used in architectural applications, such as window frames, door frames, roofing, and siding. Its corrosion resistance and ability to be colored make it a popular choice for decorative elements as well.
Aerospace: Anodized aluminum is used in the aerospace industry for its lightweight, corrosion resistance, and electrical conductivity. It is commonly used in aircraft structures, landing gear, and interior components.
Automotive: Anodized aluminum is used in the automotive industry for its corrosion resistance and aesthetic appeal. It is commonly used in exterior trims, wheels, and engine components.
Electronics: Anodized aluminum is commonly used in the electronics industry for its electrical conductivity, thermal properties, and aesthetic appeal. It is used in devices such as smartphones, tablets, laptops, and audio equipment.
Consumer goods: Anodized aluminum is used in a variety of consumer goods, including kitchenware, jewelry, and sporting equipment. Its durability and aesthetic appeal make it a popular choice for high-end products.
Medical equipment: Anodized aluminum is used in medical equipment for its biocompatibility, corrosion resistance, and ability to be sterilized. It is commonly used in surgical instruments, orthopedic implants, and diagnostic equipment.
We can supply the base material of anodized aluminum, and various series of base materials are available. IF YOU NEED, CONTACT US PLEASE!
Contact Us!
E-mail: lomialuminum@gmail.com
Tel Whatsapp: +86 19339942739
Click our website: https://www.lomialuminium.com/aluminum-sheet-price/
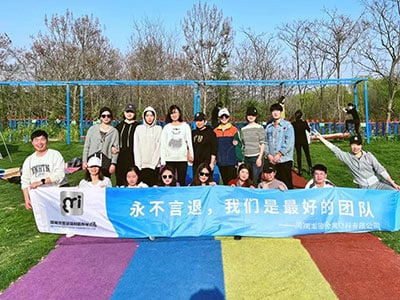