A5052 VS 5052
A5052 and 5052 are both aluminum alloys, but their chemical compositions are slightly different. A5052 alloy contains some magnesium and chromium elements, which makes its strength and corrosion resistance slightly better than that of 5052 aluminum alloy.
Specifically, the magnesium content in A5052 aluminum alloy is about 0.1% to 0.8% higher than that of 5052, and the chromium content is also slightly higher, about 0.15% to 0.35%. The addition of these elements makes A5052 aluminum alloy have better strength and corrosion resistance than 5052 aluminum alloy, especially in seawater environments.
In addition, due to the higher magnesium content in A5052 aluminum alloy, its weldability and workability may be slightly reduced, and more attention needs to be paid during welding and processing operations. In some special application areas, it may be necessary to choose the appropriate material based on the actual situation.
Parameters of A5052 Materials
Density: 2.68 g/cm³
Melting point: 607°C (1125°F)
Tensile strength: 215 MPa (31,000 psi)
Yield strength: 160 MPa (23,000 psi)
Modulus of elasticity: 70 GPa (10.1 x 10^6 psi)
Poisson’s ratio: 0.33
Thermal conductivity: 138 W/m-K (80 Btu/ft-hr-°F)
Coefficient of thermal expansion: 23.8 x 10^-6 /K (13.2 x 10^-6 /°F)
Electrical conductivity: 38% IACS (International Annealed Copper Standard)
Corrosion resistance: Excellent, particularly in seawater or salt spray environments.
A5052 material properties:
High Strength:
A5052 aluminum alloy is a high strength material and can be used to manufacture components that require high strength materials.
Good Machinability:
A5052 aluminum alloy has good machinability and can be machined using various methods such as rolling, stretching, extruding, deep drawing, and welding.
Corrosion Resistance:
A5052 aluminum alloy has excellent corrosion resistance, particularly in seawater or salt spray environments.
Lightweight:
A5052 aluminum alloy is a lightweight material, making it suitable for use in applications where weight is a critical factor.
Formability:
A5052 aluminum alloy has excellent formability and can be easily shaped into complex parts.
Weldability:
A5052 aluminum alloy has good weldability and can be welded using various methods such as gas tungsten arc welding (GTAW), gas metal arc welding (GMAW), and resistance welding.
Surface Finish:
A5052 aluminum alloy has a smooth surface finish, making it suitable for applications where appearance is important.
Electrical Conductivity:
A5052 aluminum alloy has good electrical conductivity, making it suitable for use in electrical and electronic applications.
Applications
A5052 aluminum alloy has been widely used in various fields due to its excellent physical and chemical properties. Here are some common application areas:
Automotive industry: A5052 aluminum alloy can be used to manufacture car bodies, wheels, engine covers, and other parts. Due to its lightweight, high strength, and good corrosion resistance, it has become an important material in the automotive industry.
Aerospace industry: A5052 aluminum alloy, due to its lightweight and high strength, can be used to manufacture structural components, fuselages, fuel tanks, and other parts of aircraft and spacecraft.
Electronics industry: A5052 aluminum alloy, due to its excellent electrical conductivity and corrosion resistance, is commonly used in the manufacture of electronic components, heat sinks, and housings.
Military industry: A5052 aluminum alloy can be used in the manufacture of military applications such as ships, equipment, and weapon components. Due to its good corrosion resistance, it can be used in sea-based military equipment.
Construction industry: A5052 aluminum alloy can be used in the manufacture of building shells, roofs, curtain walls, and other components. Due to its lightweight, corrosion resistance, and ease of processing, it is increasingly valued in the construction industry.
Contact Us!
E-mail: lomialuminum@gmail.com
Tel Whatsapp: +86 19339942739
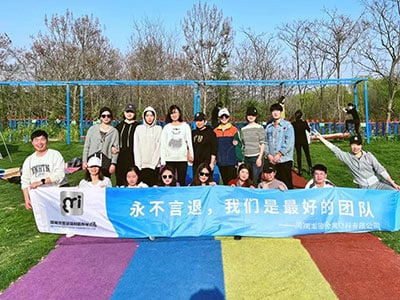